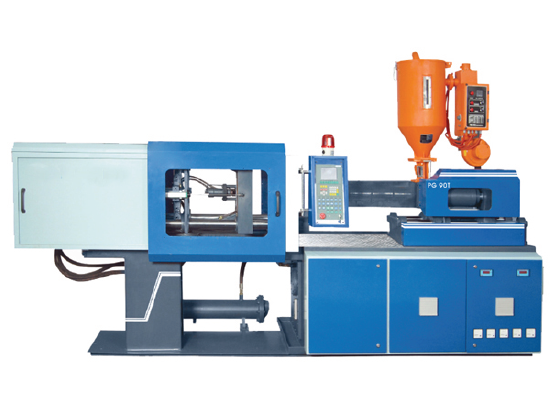
Injection Molding
Injection molding is a combination of plastic injection molding and blow molding that produces hollow, thin-walled plastic containers that are more compact and do not come with handles.
This molding method is quick and gives more precision. Molded pieces have safety enclosures similar to pill bottles, a threaded neck for screw-on lids, and thin but sturdy walls.
Manufacturing Process
What is the manufacturing process?
Injection molding is two forming processes combined into one.
Formation of Parison
A thermoplastic preform is heated until it melts and is then injected around a hollow mandrel known as a blow stem to create a plastic parison.
Placement
The newly produced parison, still encircling the stem, is put into the blow molding chamber while it is semi-cured but still flexible and bendable.
Plastic Elongation
The plastic is subsequently compelled to stretch to the product’s intended size by the steel blow stem, which will also boost the product’s overall effectiveness.
Air Injection
The hollow blow stem allows compressed air to be introduced into the parison. To take shape, the nearly-molten plastic blasts against the mold cavity’s walls and expands like a balloon.
Ejection
The freshly made plastic container is removed from the mold after it has cooled and hardened. It also doesn’t require trimming and has a uniform design.
Material Used
What are the materials used in blow molding?
Typical materials used:
- Polypropylene (PP)
- Polyethylene (PE)
- Polyvinyl Chloride (PVC)
- Polyethylene Terephthalate Glycol (PETG)
What do we inject mold?
We inject mold caps, closures, spoons, jars, and containers.