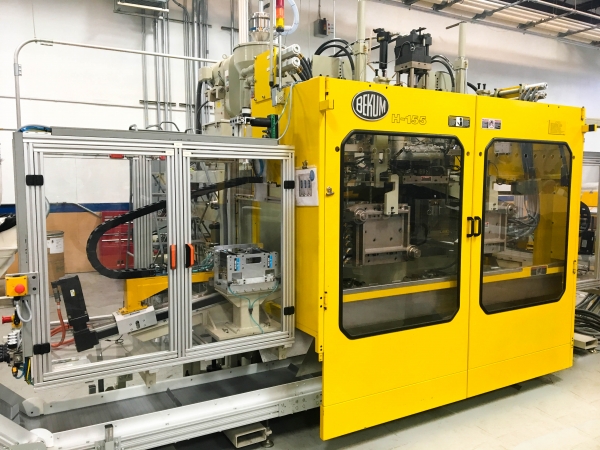
Blow Molding
Extrusion Blow Molding
Extrusion blow molding (EBM) involves melting plastic and extruding it into a hollow tube (parallel).
The parison is then enclosed in a water-cooled mold. Afterward, the plastic is inflated by air to take on the mold’s shape.
This versatile process allows the manufacture of necks in various materials and shapes.
Manufacturing Process
What is the blow molding manufacturing process?
On a rotating platform, blow molding takes place in two stages.
An extruder with a rotating screw feeds plastic pellets into the extruder, which, as it spins, creates enough friction to melt the pellets.
Stage 1: Perform Injection
During injection, molten plastic surrounds a core rod inside a preform mold. The preform mold determines the bottle’s final neck finish.
Stage 2: Blow Molding
The cavity mold in the second molding station captures the molded preforms captured by the core rod.
The core rod is then inflated with pressurized air, forcing the cavity mold to expand and take its shape.
Stage 3: Ejection
After cooling, the final formed containers are ejected. At the last quality check, sealed containers are blown with pressurized air to detect leaks.
Stage 4: Final Dispatch
Once the containers pass the leakage test, they are ready to be packed and shipped.
Material Used
What are the materials used in blow molding?
Typical materials used:
- Polypropylene (PP)
- Polyethylene (PE)
- Polyvinyl Chloride (PVC)
- Polyethylene Terephthalate Glycol (PETG)
What do we blow mold?
We blow mold bottles.